This article was originally published in June 2021 issue of HVR (Heating and Ventilating Review), a copy of which can be seen here.
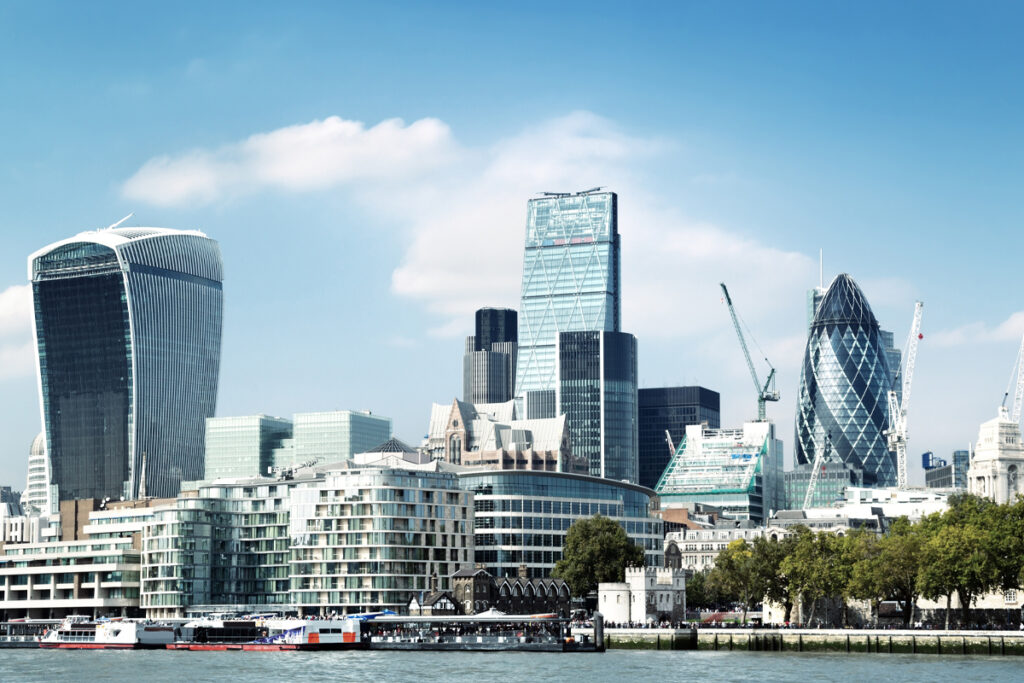
There are as many as 100 million fire and smoke dampers installed in UK buildings and each one should be tested at least annually, but BESA believes only a tiny proportion are meeting regulatory requirements. As awareness grows, can the industry cope with the potential explosion in workload?
Building owners, managers and occupiers are becoming increasingly aware of the importance of carrying out comprehensive fire safety risk assessments in the wake of the Grenfell tragedy and the new Fire Safety Bill.
Protecting a building’s fire integrity has never been more high profile and the national press is full of alarming stories about the risks faced by building occupants, but the full extent of the problem is still largely hidden. Every time an electrician drills a hole in a wall to run a cable via the shortest route from A to B, there is a strong possibility they are breaching a fire wall and, therefore, undermining the fire and smoke compartmentalisation strategy.
Fire and smoke dampers are another crucial element of fire integrity, but one that has often been ignored. However, with clients now more anxious to meet their statutory obligations, this is a once in a generation opportunity to get this aspect of fire safety firmly entrenched as a routine maintenance activity.
Market
According to the most recent market figures produced by BSRIA, there are approximately 146,000 mechanical curtain dampers and 70,000 motorised dampers installed every year. These are for new builds and replacements, which account for just 1% of the annual market, suggesting that the total number of dampers already installed in UK buildings could be as high as 100 million.
If every damper that needed to be checked was tested and maintained in line with the legislation the market would be worth at least £500 million a year.
The kitchen grease extract cleaning sector was just as ‘out of sight out of mind’ as dampers a decade ago. The specialist industry had to scale up rapidly and improve training and competence assessment to take this on after several high profile and very expensive fires flagged up the risks to owners and their insurers.
That market took at least 10 years to get to the point that it is now more or less a routine part of commercial kitchen fire protection strategies. Before that asbestos was the hidden threat inside buildings but today most building owners can point to their asbestos register when challenged.
The insurance industry is now taking a similar interest in dampers, which provide a first line of defence in stopping the spread of smoke and fire through ventilation systems. This has also prompted BESA to update its technical guidance for Fire and Smoke Damper Maintenance (VH001) which it is making widely available to support the industry’s efforts to improve the overall safety of buildings.
This guidance builds on the Association’s industry standard for ventilation safety and maintenance TR/19 and will shortly be incorporated into DW/145 which is the industry standard for the installation of dampers.
It is also in line with the Hackitt Review and the newly enacted Fire Safety Bill that continue to raise awareness. As a result, more building managers are now sub-contracting this aspect of fire compartmentalisation to specialist firms, such as Indepth Services, whose managing director Richard Norman believes the sector is at a tipping point.
“Fire Damper testing has been a legal requirement for many years, but it is only now that the penny is dropping with facilities managers and building owners that this is a crucial element of their fire safety strategy,” he says. “With only a tiny proportion of buildings fully tested and inspected, the industry will see a huge surge in demand for professional fire damper testing and repair in the next two to three years.
“It is vital, therefore, that we have proper training in place quickly to spread best practice throughout the sector in line with BESA’s guidance VH001 or an equivalent industry recognised standard. We also need to ensure that end clients understand they need comprehensive evidence that testing has taken place and not just a series of tick lists simply telling them how many dampers are installed in their building.”
Norman, who is a former chair of BESA’s Ventilation Hygiene group, says there are too many firms offering to carry out what amounts to little more than a survey that merely identifies how many dampers are there without the testing required to support fire risk assessments and satisfy building insurers.
Sophisticated
“Even in some modern, sophisticated buildings, there is little evidence that the dampers have ever been checked,” he adds. “There is widespread lack of understanding, which is similar to the kitchen grease extract market before a number of high-profile fires drove the message home.
“That market is now quite mature and the BESA guidance TR/19 provided the necessary professional standard to underpin that work.”
As with any growing market, there are a growing number of untrained, uncertified firms seeking to cash in, but they are not technically capable of providing the comprehensive service required to keep people and properties safe.
VH001 was produced in response to urgent calls for a methodology that could help the building services industry comply with the British Standard (BS9999) for fire safety in the design, management and use of buildings. It also supports the healthcare sector’s technical documents HTM 03-01 for heating and ventilation and HTM 05-02 for fire safety in healthcare premises.
BS9999 requires all installed dampers to be tested by a competent person and at regular intervals “not exceeding one year”. It also states that spring-operated dampers should be tested annually with those installed in dust-laden atmospheres checked even more regularly.
BESA’s guidance explains how dampers should be located – in line with the responsibilities of the system designer and as part of a building’s fire strategy – and accessed for testing along with the levels of competence required to carry out this work. It states that an inventory of all dampers should be created and that every manually resettable damper must be individually released to ensure the spring-loaded shutter remains operational.
All of which needs to be backed up with photographic evidence showing the condition of each damper before, during and after inspection and testing. Without that evidence, the process is not compliant.
The BESA document also sets out a comprehensive plan for providing reports to clients and any findings that need action including damaged and missing dampers. It also highlights key elements needed to put a planned maintenance regime in place for fire and smoke dampers linked to the Association’s digital maintenance tool SFG20.
This is helping to address a huge and potentially damaging impression that it is possible to reduce the frequency of damper testing to as little as every five years by carrying out risk-based assessments. This is simply wrong and dangerous but has even become quite common practice in hospitals and other healthcare facilities with obvious implications for safety.
BESA explains that one of the most important aspects of fire and smoke damper testing is pinpointing those dampers that cannot be tested – often because they cannot be found or easily reached. If you cannot test something, you must propose remedial work such as installing access panels or builders’ hatches. It is no longer acceptable – or compliant – to put in your report that a damper simply could not be tested.
Another crucial change is the requirement for the testing company to provide the client with a proposal for how this can be rectified so that 100% of dampers in an installation are checked.
Everyone has favourite examples or stories of bad practice, but it is not uncommon to hear of firms saying they could not test the dampers because they needed cleaning. If they need cleaning, then clean them and test!
Improvements
Grease extract cleaning was also hampered by the same access problems and, therefore, damper testing is already benefitting from improvements in that area with more building owners aware that it is important to install access panels and/or builders’ hatches at regular intervals.
One positive outcome from the Covid crisis is that many clients have been getting damper testing done at the same time as the building’s indoor air quality monitoring. The greater focus on building ventilation prompted by the pandemic means more end users are now aware that they actually have dampers.
Along with growing awareness of the fire safety issue, there is also more appreciation of the need for training and certification to ensure work is carried out by competent people. The ventilation hygiene industry has benefited from comprehensive training and verification of competence driven by BESA guidance. The same could now be done for damper testing based around VH001.
A crucial part of being a competent tester is the ability to address, not just those dampers that can successfully be tested, but to also provide comprehensive information about any faulty or inaccessible dampers. You should also be competent to provide feedback on any fire stopping issues that you find (including any holes that might have been drilled in a fire wall since the previous inspection) and be able to give a client a full summary and quotation so they can be compliant with legislation.
Testing which fails to show what is wrong and how to put it right, is pointless. The industry training course needs to incorporate these vital areas as well as how to successfully test a damper.
The size of the market and the life safety importance of this work should provide the necessary incentive for many employers to make the necessary investment in training and recruitment to make sure the damper industry can collectively rise to this challenge.