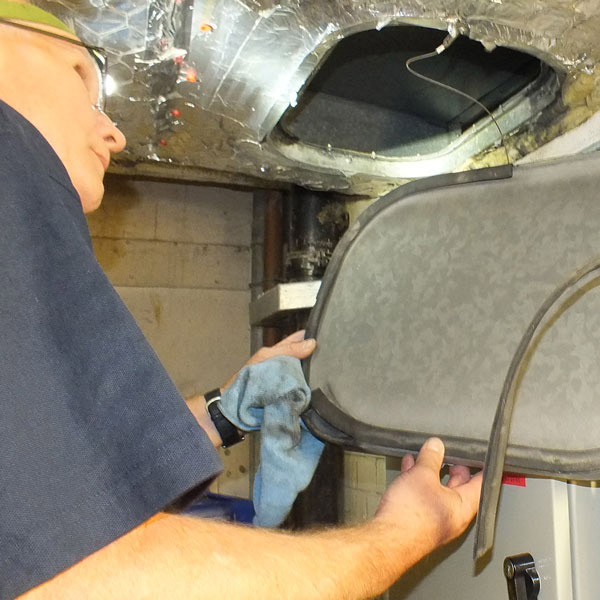
Many building owners and managers are still putting their occupants at risk by failing to have fire and smoke dampers correctly tested, according to BESA members.
Despite growing awareness of fire safety issues in general, many building operators remain confused about their responsibilities to maintain a sound working system.
The Regulatory Reform (Fire Safety) Order (RRO), which came into force in 2006, stipulates that a “responsible person” must ensure ALL components of the fire safety system in a building are kept in “efficient working order” and “good repair”. They must carry out a fire safety risk assessment and then put a planned maintenance regime in place.
Failure to do so can lead to a fine of £10,000 and two years in prison for the designated responsible person – as well as closure of the building – yet many companies remain in breach of the legislation because they ignore hidden elements of the passive fire protection.
“Ventilation ductwork is a major potential weak spot in any fire strategy because it contains critical fire safety equipment that is out of sight and is, therefore, regularly overlooked,” said Indepth managing director Richard Norman, who was chair of the BESA ventilation hygiene group for four years.
Regularly
“Under the terms of the relevant UK standard BS9999, dampers should be tested at least once a year – and in ventilation systems likely to accumulate dust more quickly or in other types of high-risk buildings tests should be carried out even more regularly,” he said.
A fire damper survey is the first step towards achieving a fire damper testing regime in line with the legal requirements of the RRO. Once they are located, dampers need to be inspected. A visual assessment will highlight any damage or anything that might prevent the damper from closing properly in the event of a fire.
Some building owners are now commissioning ‘asset registers’ to establish how many dampers they have, but this can only ever be a first step and does not make the building compliant with fire legislation.
“If you are going to all the trouble and expense of having a damper survey, why not have the dampers tested at the same time? This is a far more efficient and effective process that, as well as saving clients’ money by combining the two activities, helps them comply with legislation more quickly,” explained Mr Norman.
He also criticised the practice of simply checking the dampers were in place and then issuing a certificate.
“In the past, ‘tests’ were often little more than visual verifications followed by the issuing of a certificate that did nothing to make people safer. Fortunately, we are starting to see an improvement in the professionalism of the industry and the sooner this stops being little more than a ‘tick box’ exercise the better.”
Each damper should be drop tested and then reset to open. A full test report should then be issued including photographs of each tested damper in the open and dropped position. At this point, the specialist carrying out the test must notify the building operator of any remedial work that may be needed, accompanied by a schedule of works and associated costs. The remedial work must be undertaken in order for the building to comply with the RRO.
This article was originally published in Issue 13 of the Your BESA magazine. A full copy can be seen here.